All about Alcast Company
All about Alcast Company
Blog Article
An Unbiased View of Alcast Company
Table of ContentsNot known Details About Alcast Company The Single Strategy To Use For Alcast CompanyAlcast Company Things To Know Before You BuyOur Alcast Company DiariesSome Known Facts About Alcast Company.4 Easy Facts About Alcast Company ShownThe Main Principles Of Alcast Company

If you believe that a wrought alloy may be the most effective for your task, have a look at a few of our posts that explain more regarding details wrought alloys, such as Alloy 6061 and Alloy 6063. On the other hand, if you assume a cast alloy would be much better for you, you can find out more about some cast alloys in our Alloy 380 and Alloy 383 short articles (coming soon).
Some Known Factual Statements About Alcast Company
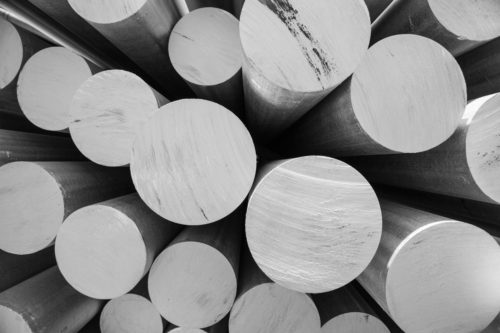
Having the experience and sector understanding to engineer your spreadings for optimum manufacturing and quality outcomes will enhance the task. Making aluminum castings requires a complex set of processes to accomplish the ideal outcomes. When deciding on a new light weight aluminum foundry to partner with, ensure they have extensive industry experience and are well-informed regarding all aspects of the light weight aluminum casting procedure: design, production, material evaluation, and item testing.
(https://www.callupcontact.com/b/businessprofile/Alcast_Company/9564446)The foundry needs to likewise have a tried and tested track record of supplying outstanding products that fulfill or surpass customer assumptions. Quality assurance ought to additionally be at the top of your checklist when selecting an aluminum factory. By collaborating with a certified shop who adheres to the standards for quality assurance, you can safeguard the honesty of your product and guarantee it fulfills your specs.
Some Known Factual Statements About Alcast Company
By choosing a company who supplies solutions that satisfy or exceed your item needs, you can be sure that your project will be finished with the utmost accuracy and effectiveness. Various components need different manufacturing strategies to cast aluminum, such as sand casting or pass away casting.
Die spreading is the name provided to the procedure of producing complex steel parts with usage of molds of the part, likewise known as passes away. It produces even more elements than any various other process, with a high degree of precision and repeatability. There are three sub-processes that drop under the category of die casting: gravity pass away casting (or long-term mold and mildew casting), low-pressure die spreading and high-pressure die casting.
No matter the sub-process, the die spreading procedure can be broken down into 6 steps. After the pureness of the alloy is tested, dies are created. To prepare the needs spreading, it is very important that the passes away are clean, to ensure that no deposit from previous productions stay. After cleaning, the ejection lubrication is put on the die to ensure a smooth release.
The pure steel, additionally known as ingot, is added to the heating system and maintained the molten temperature level of the metal, which is then transferred to the injection chamber and infused right into the die (aluminum foundry). The stress is then preserved as the steel solidifies. As soon as the metal solidifies, the cooling procedure begins
The 4-Minute Rule for Alcast Company
The thicker the wall surface of the part, the longer the cooling time as a result of the quantity of indoor steel that additionally requires to cool. After the component is fully cooled, the die cuts in half open and an ejection device presses the element out. Complying with the ejection, the die is closed for the following shot cycle.
The flash is the added material that is cast throughout the process. Deburring gets rid of the smaller sized items, called burrs, after the cutting procedure.
The Buzz on Alcast Company
Today, top producers utilize x-ray screening to see the whole interior of components without cutting right into them. To obtain to the ended up product, there are three primary alloys utilized as die casting product to select from: zinc, light weight aluminum and magnesium.
Zinc is one of websites the most used alloys for die spreading due to its reduced price of raw products (aluminum casting manufacturer). Its rust resistance additionally allows the components to be long long-term, and it is one of the extra castable alloys due to its reduced melting factor.
Some Known Details About Alcast Company
As pointed out, this alloy is just one of one of the most generally used, yet makes will, at times, choose light weight aluminum over zinc because of light weight aluminum's manufacturing advantages. Light weight aluminum is extremely economical and among the much more functional alloys. Aluminum is used for a variety of different products and industries anything from home window frames to aerospace products.
Report this page